Development of anti-fouling PVDF membranes by phase inversion membrane bioreactors.
Membrane distillation (MD) is a technique involving the Non-isothermal transport of fluids, especially water, through membranes. The major barriers hindering the full commercialization of this process include MD membrane and module design, membrane pore wetting, low permeate flow rate, flux decay with time, as well as uncertain energy and economic costs. These challenges have attracted scientists and engineers striving for the best membrane performance, module and process design, among which the selection of membrane materials was the most important. A key influence for the MD membrane is the fabrication procedures which influence the morphology and porosity, thereby defining the performance efficiency of fabricated membranes.
Polyvinylidenefluoride (PVDF) remains among the preferred options for MD membrane materials, because of the ease of PVDF dissolution in common organic solvents. As a result, porous PVDF membranes can be produced via phase inversion method. PVDF is a semi-crystalline fluoropolymer thermoplastic obtained by polymerizing vinylidene fluoride units. The major factor determining the type of phase separation that occurs for a system involving a semi crystalline polymer, such as PVDF, is the miscibility of the system, which is associated with the strength of polymer–diluents interactions. PVDF porous membranes can be easily produced by phase separation (i.e. phase inversion) process, simply immersing the cast solution film in a coagulant bath (i.e. non-solvent, frequently water). In this case, membrane porosity is controlled by additives in the casting solution (e.g., pore-forming agents) or by replacing water in the coagulation bath with a different non-solvent medium.
Additives can be used to impart pores, hydrophilicity, hydrophobicity, mechanical strength, antifouling properties and surface modification. A pore forming agent though diverse in the chemical nature is unanimous in it functional role of imparting a porous nature or enhancing the interconnectivity between pores. Pore forming agents do impart multifunctional effects, which may be synergistic or detrimental in end properties. A pore former can increase solution viscosity or accelerate the phase inversion process, to improve the membrane morphology, and to enhance the membrane separation as well as the performance.
In our research group, we are currently investigating the role of novel additives and process parameters in pore formation and also their influence on key membrane parameters such as morphology, hydrophobicity, Liquid entry Pressure [LEP], and pore size distribution [PSD], together with many other parameters such as mechanical strength and crystallinity. The final goal of the study is to identify and bring to practical application, suitable membranes which will stand the intricate demands of Membrane Distillation.
Various sophisticated analytical tools such as the Optical microscope and Scanning Electron Microscope [SEM] are used to unfold the structural constitution of the fabricated flat sheet and hollow fiber membranes. The pore characteristics are investigated using the Capillary Flow Porometry [CFP] and the surface interactions with water are evaluated using the Contact Angle Measurements.
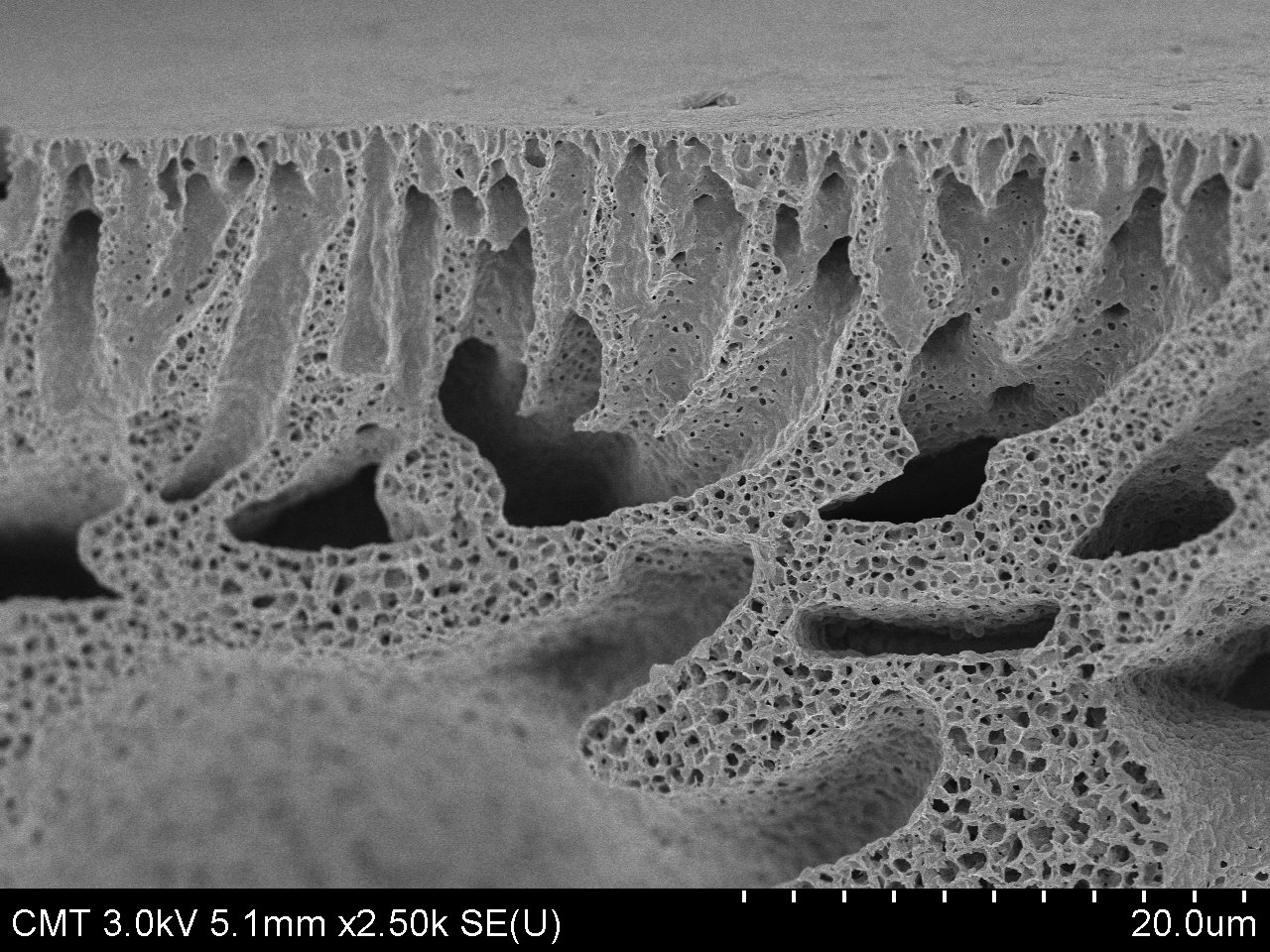
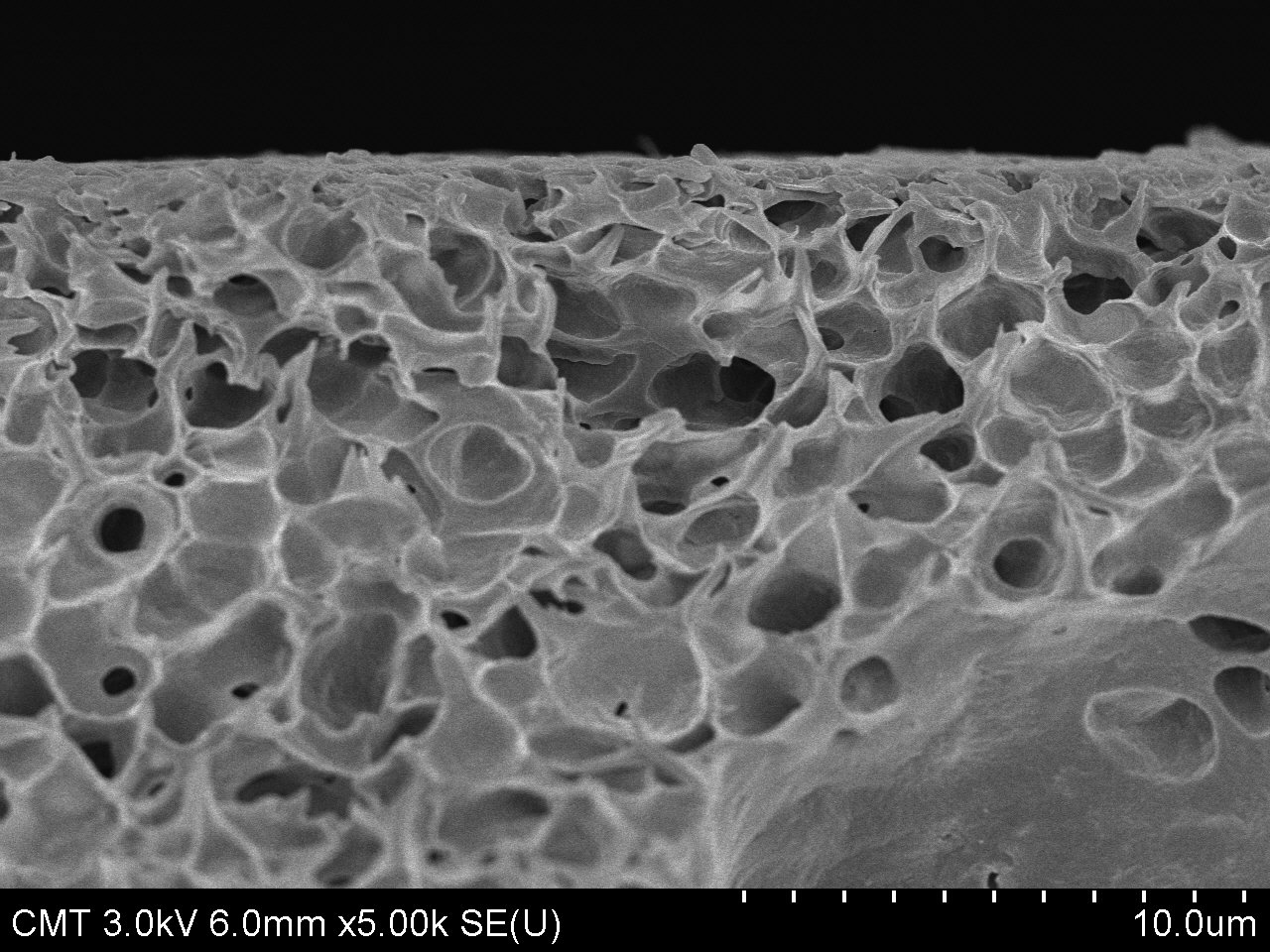
Development of corrugated PVDF membranes by phase inversion membrane bioreactors
Membrane bioreactor (MBR) is the combination of a suspended growth bioreactor with a membrane process (e.g. ultrafiltration or microfiltration). It is now widely used for treatment of municipal and industrial wastewater. Even only a decade ago, membranes bioreactors were still an emerging technology and relatively novel within the municipal wastewater treatment industry. MBR processes, when used with domestic wastewater, can produce high quality effluent enough to be discharged to coastal, surface or brackish waterways or to be reclaimed for urban irrigation. Moreover, MBR has many other advantages over the conventional processes include small footprint, and easy upgrade of old wastewater treatment plants. The membranes at the heart of the MBR technology easily become clogged with microorganisms and algae that grow on them – a process known as biofouling. Nothing can get through the membrane’s pores, making it no use as a filter for wastewater – so treatment has to stop for the membrane to be either cleaned or replaced. The loss of productivity, along with the cost of the treatment chemicals or new membranes, reduces the cost effectiveness of the MBR. A membrane that prevented biofouling could make MBRs a far more attractive option for water treatment. That is where our novel membrane comes in.
We have created an Anti-fouling membrane that is highly resistant to biofouling and also improves the through-flow of water. This was achieved by improving the membrane structure, porosity, and surface chemistry. The developed membranes were fully characterized before put into the test. This included, to mention some, contact angle, scanning electron microscopy, porosity and pore size distribution.

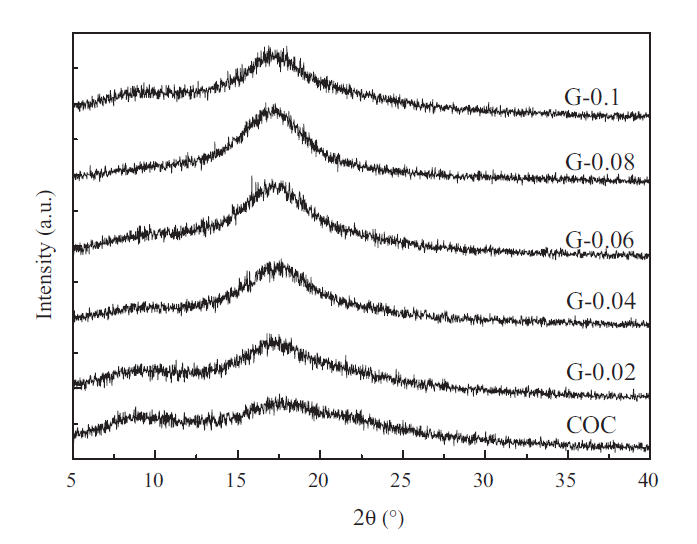
PVDF membrane made using VIPS and NIPS pathways for distillation
Phase inversion is one of the popular membrane fabrication techniques for membrane distillation applications. A recent study showed the importance of the solution composition pathway in the ternary phase diagram on the hydrophobicity of the resultant membrane. The pathway is highly dependent on the membrane fabrication route, having on one side the complete non-solvent induced phase separation (NIPS) and on the other side the vapor induced phase separation (VIPS). These two extremes lead to two different membranes with different surface and in-situ properties. The NIPS membranes are characterised by low contact angle with low pore size, while VIPS membranes are characterised by high contact angle and high pore size.
The aim of our study is to tune the membrane properties by combining the NIPS and VIPS membrane fabrication techniques to achieve a superhydrophobic membrane with low bubble point diameter and a narrow pore size distribution. In this study the polymer of choice is Polyvinylidene fluoride (PVDF) and the solvent is Dimethylacetamide (DMAC). Water is used as a strong non-solvent for NIPS. We investigate the role of casting thickness together with the other variables in NIPS and VIPS to obtain the desired membrane properties. The VIPS process is carried out in a humidity controlled chamber.
An important part of the study is membrane characterisation. Surface scanning electron microscope (SEM) images are taken for all membranes to reveal their surface morphology and structure. Mean flow pore size, maximum pore size and the pore size distribution are measured using a capillary flow porometer. Contact angle measurements of deionised water are taken using a contact angle goniometer.
Preliminary results of the study showed superhydrophobic membranes could be obtained via the VIPS process with contact angles in the range of 140-145º. However, maximum pore size and pore size distribution of these membranes are still relatively high, in the order of 10-20 um, which renders them useless for membrane distillation (MD) applications. Currently the group is optimising the fabrication process to minimise the pore sizes and ultimately high flux and less wetting membranes for MD applications.
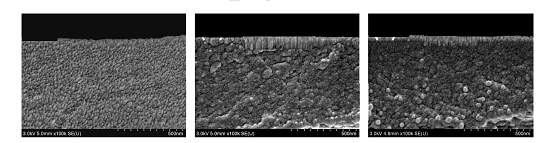